
Toyota Camry
XV30 (2002–2006) Service Manual
Introduction
Repair instruction
Repair instruction
PRECAUTION
1. BASIC REPAIR HINT
a. HINTS ON OPERATIONS
Basic repair hint
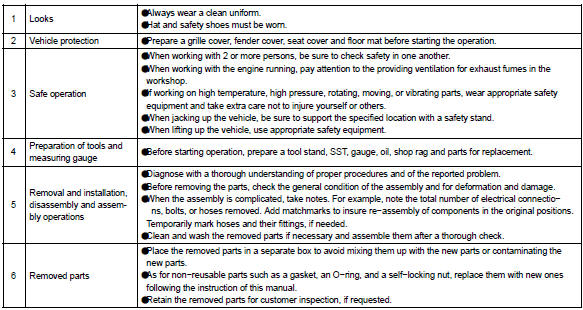
b. JACKING UP AND SUPPORTING VEHICLE
1. Care must be taken when jacking up and supporting the vehicle. Be sure to
lift and support the
vehicle at the proper locations .
c. PRECOATED PARTS
- Precoated parts are bolts, nuts, etc. that are coated
with a seal lock adhesive at the factory.
- If a precoated part is retightened, loosened or
moved in anyway, it must be recoated with the specified
adhesive.
- When reusing precoated parts, clean off the old
adhesive and dry the part with compressed air.
- Then apply new seal lock adhesive appropriate to
the bolt, nut, or threads.
NOTICE:
Perform the torque with the lower limit value of the torque
tolerance.
4. Some seal lock agents harden slowly. You may
have to wait for the seal lock agent to harden.
Precoated parts
d. GASKETS
1. When necessary, use a sealer on gaskets to prevent leaks.
e. BOLTS, NUTS AND SCREWS
1. Carefully follow all the specifications for tightening torques. Always
use a torque wrench.
f. FUSES
1. When replacing fuses, be sure that the new fuse
has the correct amperage rating. DO NOT exceed
the rating or use one with a lower rating.
Fuses
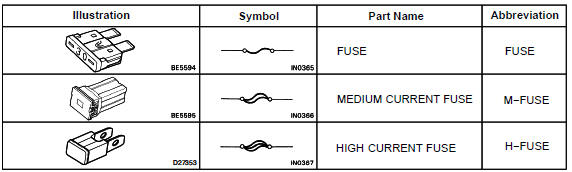
g. CLIPS
1. The removal and installation methods of typical clips used in body parts
are shown in the table
below.
HINT:
If clips are damaged during a procedure, always replace the damaged clip with a
new clip.
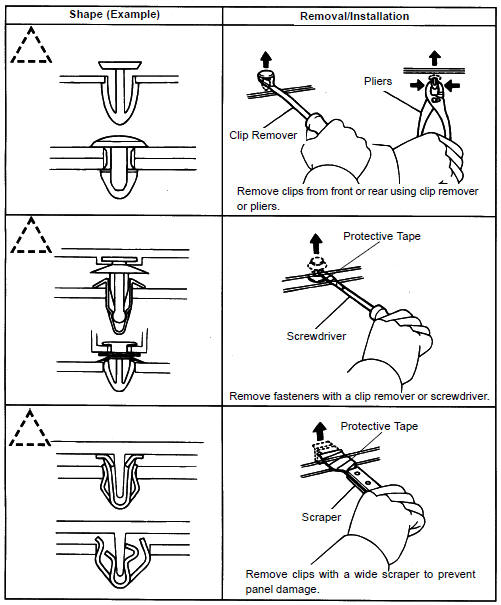
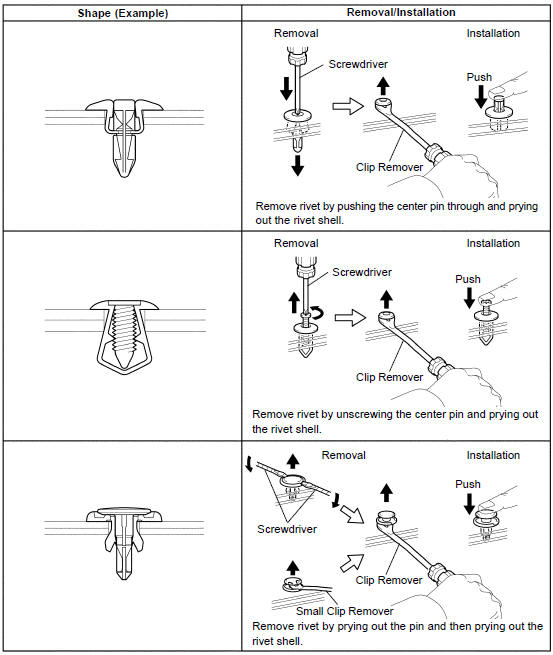
h. REMOVAL AND INSTALLATION OF VACUUM HOSES
1. To disconnect vacuum hose, pull and twist from the
end of the hose. Do not pull from the middle of the
hose as this may cause damage.
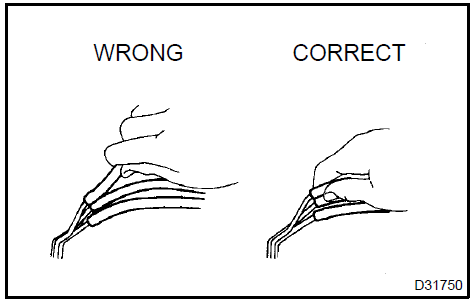
- When disconnecting vacuum hoses, use tags to
identify where they should be reconnected.
- After completing the job, double check that the vacuum
hoses are properly connected. The label under
the hood shows the proper layout.
- When using a vacuum gauge, never force the hose
onto a connector that is too large. Use a step−down
adapter for adjustment. Once the hose has been
stretched, it may leak air.
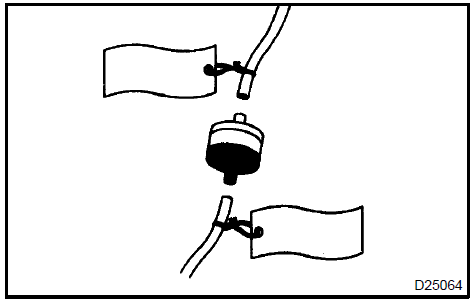
i. TORQUE WHEN USING TORQUE WRENCH WITH EXTENSION
TOOL
- If SST or an extension tool is combined with the
torque wrench to extend its length, do not tighten
the torque wrench to the specified torque values in
this manual. The actual torque will be excessive.
- Use the formula below to calculate special torque
values for situations where SST or an extension tool
is combined with the torque wrench.
- Formula: T’=T x L2/(L1 + L2)
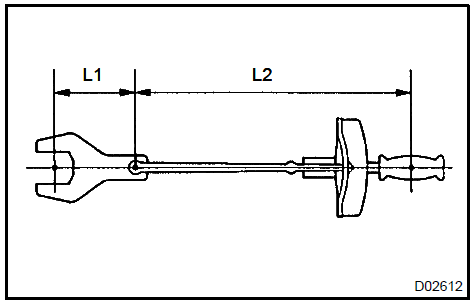
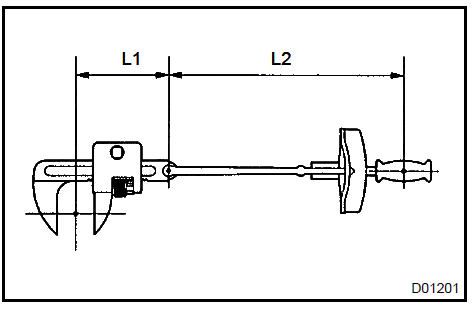

2. FOR VEHICLES EQUIPPED WITH SRS AIRBAG AND SEAT BELT PRETENSIONER
HINT:
The CAMRY is equipped with a Supplemental Restraint System (SRS) and seat belt
pretensioner.
Failure to carry out the service operations in the correct sequence could cause
the SRS to unexpectedly
deploy during servicing and lead to serious injury.
Furthermore, if a mistake is made when servicing the SRS, it is possible that
the SRS may fail to operate
properly. Before servicing (including removal or installation of parts,
inspection or replacement), be sure to
read the following section carefully.
a GENERAL NOTICE
- Malfunction symptoms of the SRS are difficult to confirm so the
Diagnostic Trouble Codes (DTCs)
become the most important source of information when troubleshooting. When
troubleshooting
the SRS, always check the DTCs before disconnecting the battery.
- To avoid serious injury, servicing the SRS must be started 90 seconds
after:
- The ignition switch is turned to the LOCK position.
- The negative (−) terminal cable is disconnected from the battery.
(The SRS is equipped with a back−up power source. If work is started within
90 seconds of disconnecting
the negative (−) terminal cable from the battery, the SRS may deploy).
Disconnecting the negative (−) terminal cable will erase clock memory and audio
system presets.
Mark down data as necessary before disconnecting the cable.
CAUTION:
Never use a back−up power source (battery or other) avoid erasing system memory.
The back−up
power source may power the SRS, leading to a possible SRS and cause it to
deploy.
- In minor collisions where the SRS does not deploy, the horn button
assembly, instrument panel
passenger airbag assembly front seat airbag assembly, curtain shield airbag
assembly and seat
belt pretensioner should be inspected before further use of the vehicle (See
pages 60−27,
60−40, 60−53, 60−47 and 61−7).
- Never use SRS parts from another vehicle. When replacing parts, use new
parts.
- (Before repairs, remove the airbag if impacts are likely to be
applied to the during
repairs.
- Never disassemble and repair the airbag assembly, horn button
assembly, instrument
panel passenger airbag assembly front seat airbag assembly, curtain shield
airbag assembly or
seat belt pretensioner.
- Replace the center airbag assembly, side airbag assembly,
horn button assembly
or the instrument panel passenger airbag assembly front seat airbag assembly
or curtain shield
airbag assembly: 1) if damage has occurred from being dropped, or 2) if
there are cracks, dents
or other defects in the case, bracket or connector.
- Do not directly expose the airbag assembly, front seat airbag
assembly, curtain shield
airbag assembly the horn button assembly, the instrument panel passenger
airbag assembly or
the seat belt pretensioner to hot air or flames.
- Use a voltmeter/ohmmeter with high impedance (10 kW/V minimum) for
troubleshooting electrical
circuits.
- Information labels are attached to the SRS components. Follow the
instructions on the labels.
- After work on the SRS is completed, check the SRS warning light .
b. SPIRAL CABLE (in Combination Switch)
1. The steering wheel must be fitted correctly to the
steering column with the spiral cable at the neutral
position, otherwise cable disconnection and other
problems may occur. Refer to page 60−34 concerning
the correct installation of the steering wheel.
Spiral cable
c. HORN BUTTON ASSEMBLY (with Airbag)
- When removing the horn button assembly or handling a new horn button, it
should be placed with
the pad surface facing up. See illustration below.
Placing the horn button with the pad surface facing down may lead to a
serious accident if the
airbag accidently inflates. Also, do not place anything on top of the horn
button.
- Never measure the resistance of the airbag squib. This may cause the
airbag to inflate, which
could cause serious injury.
- Grease or detergents of any kind should not be applied to the steering
wheel pad.
- Store the horn button assembly where the ambient temperature remains
below 93°C (200°F),
has low humidity and is away from electrical noise.
- When using electric welding anywhere on the vehicle, disconnect the
airbag ECU connectors
(4 yellow pins). These connectors contain shorting springs. This feature
reduces the possibility
of the airbag or seat belt pretensioner deploying due to currents entering
the squib wiring.
- When disposing of the vehicle or the horn button assembly by itself, the
airbag should be inflated
using an SST before disposal . Perform the operation in a safe place away
from
electrical noise.
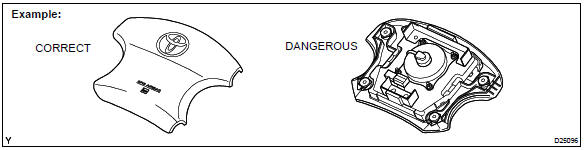
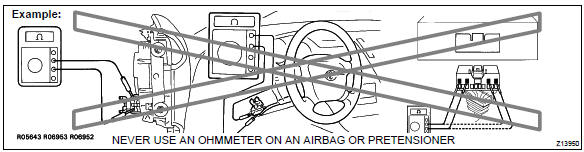
d. INSTRUMENT PANEL PASSENGER AIRBAG ASSY
- Always place a removed or new instrument panel passenger airbag assembly
with the airbag
inflation direction facing upward.
Placing the airbag assembly with the airbag inflation direction facing
downward could cause a
serious accident if the airbag inflates.
- Never measure the resistance of the airbag squib. This may cause the
airbag to inflate, which
could cause serious injury.
- Grease or detergents of any kinds should not be applied to the
instrument panel passenger airbag
assembly.
- Store the airbag assembly where the ambient temperature remains below
93°C (200°F), has low
humidity and away from electrical noise.
- When using electric welding anywhere on the vehicle, disconnect the
airbag ECU connectors
(4 yellow pins). These connectors contain shorting springs. This feature
reduces the possibility
of the airbag deploying due to currents entering the squib wiring.
- When disposing of a vehicle or the airbag assembly unit by itself, the
airbag should be deployed
using SST before disposal .
Activate in a safe place away from electrical noise.
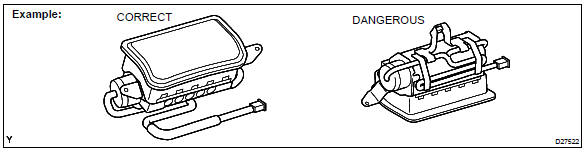
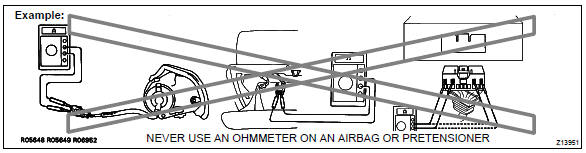
e. FRONT SEAT AIRBAG ASSEMBLY
- Always place a removed or new front seat airbag assembly with the airbag
inflation direction facing
upward. Placing the airbag assembly with the airbag inflation direction
facing downward
could cause a serious accident if the airbag deploys.
- Never measure the resistance of the airbag squib. This may cause the
airbag to inflate, which
is very dangerous.
- Grease should not be applied to the front seat airbag assembly, and the
airbag door should not
be cleaned with detergents of any kind.
- Store the airbag assembly where the ambient temperature remains below
93°C (200°F), without
high humidity and away from electrical noise.
- When using electric welding anywhere on the vehicle, disconnect the
airbag ECU connectors
(2 yellow pins). These connectors contain shorting springs. This feature
reduces the possibility
of the airbag deploying due to currents entering the squib wiring.
- When disposing of a vehicle or the airbag assembly unit, the airbag
should be deployed using
SST before disposal .
Activate in a safe place away from electrical noise.
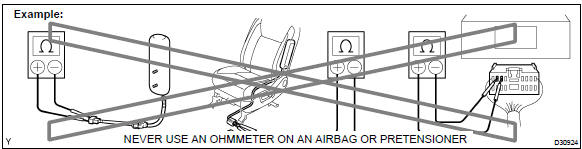
f. CURTAIN SHIELD AIRBAG ASSEMBLY
- Always place the removed or new curtain shield airbag assembly in a
clear plastic bag, and keep
it in a safe place.
NOTICE:
Plastic bag is not re−useable.
CAUTION:
Never disassemble the curtain shield airbag assembly.
- Never measure the resistance of the airbag squib. This may cause the
airbag to inflate, which
is very dangerous.
- Grease should not be attached to the curtain shield airbag assembly, and
the surface should not
be cleared with detergents of any kind.
- Store the airbag assembly where the ambient temperature remains below
93°C (200°F), without
high humidity and away from electrical noise.
- When using electric welding anywhere on the vehicle, disconnect the
airbag ECU connectors
(2 yellow pins). These connectors contain shorting springs. This feature
reduces the possibility
of the airbag deploying due to currents entering the squib wiring.
- When disposing of a vehicle or the curtain shield airbag assembly unit,
the airbag should be
deployed using SST before disposal .
- Activate in a safe place away from electrical noise.
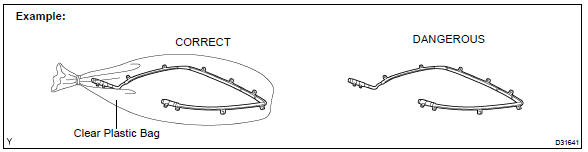
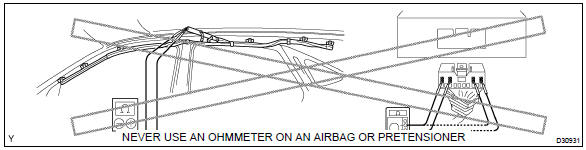
g. SEAT BELT PRETENSIONER
- Never measure the resistance of the seat belt pretensioner (This may
cause the seat belt pretensioner
to activate, which is very dangerous).
- Never disassemble the seat belt pretensioner.
- Never install the seat belt pretensioner on another vehicle.
- Store the seat belt pretensioner where the ambient temperature remains
below 80°C (176°F)
without high humidity and away from electrical noise.
- When using electric welding anywhere on the vehicle, disconnect the
airbag ECU connectors
(2 yellow pins). These connectors contain shorting springs. This feature
reduces the possibility
of the airbag deploying due to currents entering the squib wiring.
- When disposing of a vehicle or the seat belt pretensioner unit, the seat
belt pretensioner should
be activated before disposal . Perform the operation in a safe place away
from
electrical noise.
- The seat belt pretensioner is hot after being activated, so allow some
time for it to cool down sufficiently
before disposal. Never apply water to cool down the seat belt pretensioner.
- Oil or water should not be put on the front seat outer belt, and the
front seat outer belt should
not be cleaned with detergents of any kind.
Seat belt pretensioner
h. AIRBAG ASSEMBLY
- Never reuse an airbag assembly that has been involved in a
collision where the SRS has
deployed.
- The connectors to the airbag assembly should be connected or
disconnected with the
mounted on the floor. If the connectors are connected or disconnected
while the airbag
assembly is not mounted to the floor, it could cause accidental
deployment of the SRS.
- Work must be started at last 90 seconds after the ignition switch is
turned to the LOCK position
and the negative (−) terminal cable is disconnected from the battery, even
if only loosening the
set bolts of the airbag assembly.
i. WIRE HARNESS AND CONNECTOR
1. The SRS wire harness is integrated with the instrument panel wire harness
assembly. All the connectors
in the system are a standard yellow color. If the SRS wire harness becomes
disconnected
or the connector becomes broken, repair or replace it.
3. ELECTRONIC CONTROL
a. REMOVAL AND INSTALLATION OF BATTERY TERMINAL
- Before performing electronic work, disconnect the
battery negative (−) terminal cable beforehand to
prevent component and wire damage caused by
accidental short circuits.
- When disconnecting and installing the terminal
cable, turn the ignition switch and lighting switch
OFF and loosen the terminal nut completely. Perform
these operations without twisting or prying the
terminal. Remove the battery cable from battery
post.
- Clock settings, radio settings, DTCs and other data
are erased when the battery cable is removed. Before
removing the battery cable, record any necessary
data.
- When disconnecting the battery’s negative (−) terminal
cable, re−initialize the following systems after
the completion of the operation.
Removal and installation of battery terminal
b. HANDLING OF ELECTRONIC PARTS
- Do not open the cover or case of the ECU unless
absolutely necessary. If the IC terminals are
touched, the IC may be rendered inoperative by
static electricity.
- To disconnect electronic connectors, pull the connector
itself, not the wires.
- Be careful not to drop electronic components, such
as s or relays. If they are dropped on a hard
floor, they should be replaced.
- When cleaning the engine with steam, protect the
electronic components, air filter and emission−related
components from water.
- Never use an impact wrench to remove or install
temperature switches or temperature s.
- When checking the continuity at the wire connector,
insert the tester probe carefully to prevent terminals
from bending.
Handling of electronic parts
4. REMOVAL AND INSTALLATION OF FUEL CONTROL PARTS
a. PLACE FOR REMOVING AND INSTALLING OF FUEL SYSTEM PARTS
- Work in a place with good air ventilation and without any ignition
sources, such as a welder, grinder,
drill, electric motor or stove.
- Never work in a place such as a pit or near a pit because vaporized fuel
will collect in those places.
b. REMOVING AND INSTALLING OF FUEL SYSTEM PARTS
- Prepare a fire extinguisher before starting operation.
- To prevent static electricity, install a ground on the fuel changer,
vehicle and fuel tank, and do
not spray the area with water. The work surface will become slippery. Do not
clean up spills with
water as this will spread and gasoline and create a fire hazard.
- Never use any electric equipment like an electric motor or a working
light, as they may create
sparks or high temperatures.
- Never use an iron hammer, as it may create sparks.
- Dispose of fuel−contaminated shop rags separately using a fire restraint
container.
5. REMOVAL AND INSTALLATION OF ENGINE INTAKE
PARTS
- If any metal particle enters the inlet pass, this may damage
the engine.
- When removing and installing the inlet system parts, cover
the openings of the removed parts and engine openings.
- Use clean shop rags, gummed tape, or other suitable
materials.
- When installing the inlet system parts, check that no metal
particles have entered the engine or the installed part.
Removal and installation of engine intake parts
6. HANDLING OF HOSE CLAMPS
- Before removing the hose, check the clamp position so
that you can restore it in the same way.
- Replace deformed or dented clamps with a new one.
- When reusing a hose, attach the clamp on the clamp track
portion of the hose.
- For a spring type clamp, you may want to spread the tabs
slightly after installation by pushing in the direction of the
arrow marks as shown in the illustration.
Handling of hose clamps
7. FOR VEHICLES EQUIPPED WITH MOBILE COMMUNICATION
SYSTEMS
- Install the antenna as far away from the ECU and s
of the vehicle electronic systems as possible.
- Install an antenna feeder at least 20 cm (7.87 in.) away
from the ECU and s of the vehicle electronic systems.
For details of the ECU and s locations, refer
to the section on applicable components.
- Keep the antenna and feeder separate from other wirings
as much as possible. This will prevent signals from the
communication equipment from affecting vehicle equipment
and vice−versa.
- Check that the antenna and feeder are correctly adjusted.
- Do not install any high−powered mobile communication
system.
For vehicles equipped with mobile communication systems
8. FOR VEHICLES EQUIPPED WITH TRACTION CONTROL
(TRAC) SYSTEM
When using a 2−wheel drum tester such as a speedometer tester,
a combination tester of speedometer and brake, chassis dynamometer,
or jacking up the front wheels and driving the
wheels, always turn the TRAC system off via the TRAC OFF
switch before testing.
NOTICE:
TRAC system OFF condition can be confirmed by the
”TRAC OFF” warning indicator light in the combination meter.
a. Confirm TRAC system is OFF
- Press the TRAC cut (”TRAC OFF”) switch to turn off
the TRAC system.
- Check if the TRAC OFF indicator light illuminates.
HINT:
The SLIP indicator light should always operate right after the
engine is restarted.
- Begin testing.
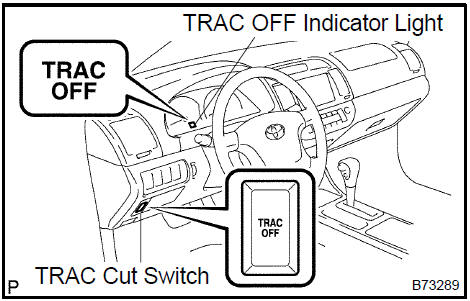
- Press the TRAC cut switch to turn on the TRAC system
and check that the TRAC OFF indicator light
turns off.
HINT:
The SLIP indicator light blinks when the TRAC system is operating.
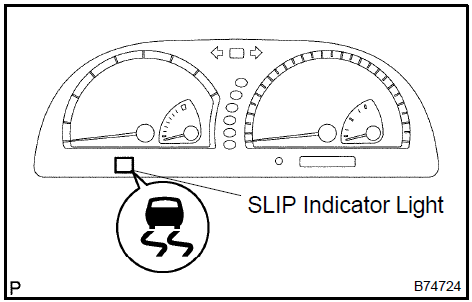
9. FOR VEHICLES EQUIPPED WITH VEHICLE SKID
CONTROL (VSC) SYSTEM
a. NOTICES WHEN USING DRUM TESTER
- Before beginning testing, disable the Vehicle Skid
Control system (VSC). To disable the VSC, turn the
ignition switch OFF and connect SST to terminals
TS and CG of DLC3.
For vehicles equipped with vehicle skid control (VSC) system
NOTICE:
- Confirm that the VSC warning light blinks.
- VSC system will be reset when the engine is restarted.
- For safety, secure the vehicle with restraint chains
while using a wheel dynamometer.
b. NOTICES OF RELATED OPERATIONS TO VSC
- Do not carry out unnecessary installation and removal
as it might affect the adjustment of VSC related
parts.
- Be sure to follow the instructions for work preparation
and final confirmation of proper operation of the
VSC system.
10. FOR VEHICLES EQUIPPED WITH CATALYTIC CONVERTER
CAUTION:
If a large amount of unburned gasoline or gasoline vapors flow into the
converter, it may cause overheat
and create a fire hazard. To prevent this, observe the following precautions.
- Use only unleaded gasoline.
- Avoid prolonged idling. Avoid idling the engine for more than 20 minutes.
- Avoid a spark jump test.
- Perform a spark jump test only when absolutely necessary. Perform this
test as rapidly as possible.
- While testing, never race the engine.
- Avoid a prolonged engine compression measurement.
Engine compression measurements must be performed as rapidly as possible.
- Do not run the engine when the fuel tank is nearly empty. This may cause
the engine to misfire and
create an extra load on the converter.
More about «Introduction»:
Repair instruction